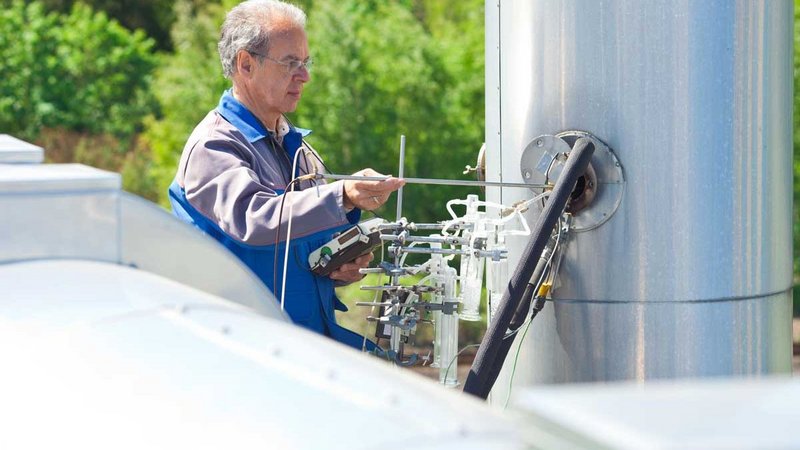
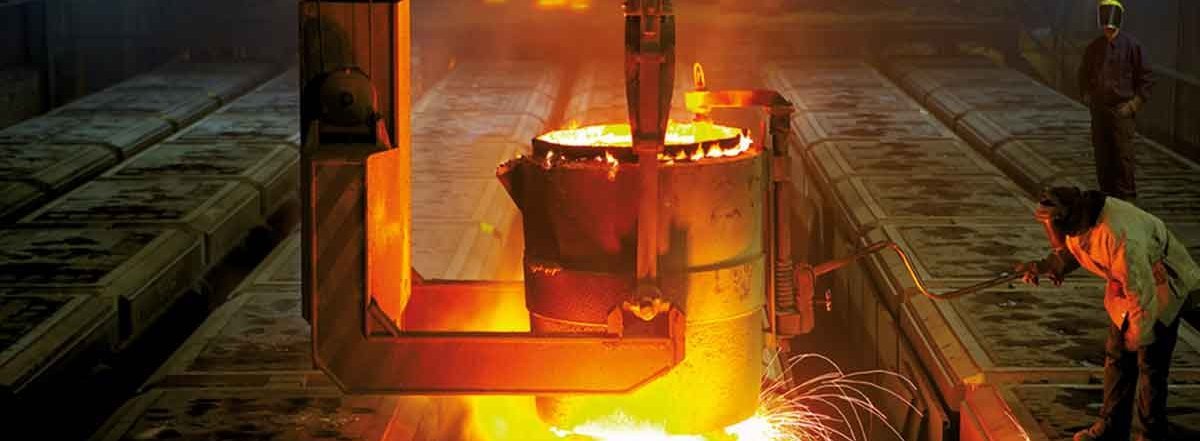
Casting clean steel: induction furnace lining systems
20 Jan 2024
Key takeaways:
- Prevent refractory inclusion defects
- Reduce gas porosity defects
- Improve as-cast quality
For more on the different types of common steel casting defects, check out our white paper.
Casting defects: the challenge
Casting defects weigh heavily on the efficiency, profitability and environmental sustainability of steel casting operations, resulting in:
- Lower yields.
- Higher production costs per piece.
- Extended lead times.
- Bottlenecks in the cleaning room.
- Higher energy consumption.
- Increased carbon footprint associated with foundry operations.
The causes of casting defects are numerous and can be found at most points in the casting process – from the furnace to the mould.
In a series of blogs – of which this is the first – we will outline what can be done at various stages of the steel casting process to ensure high-quality, clean casting. We start at the beginning, in the furnace, with refractory linings.
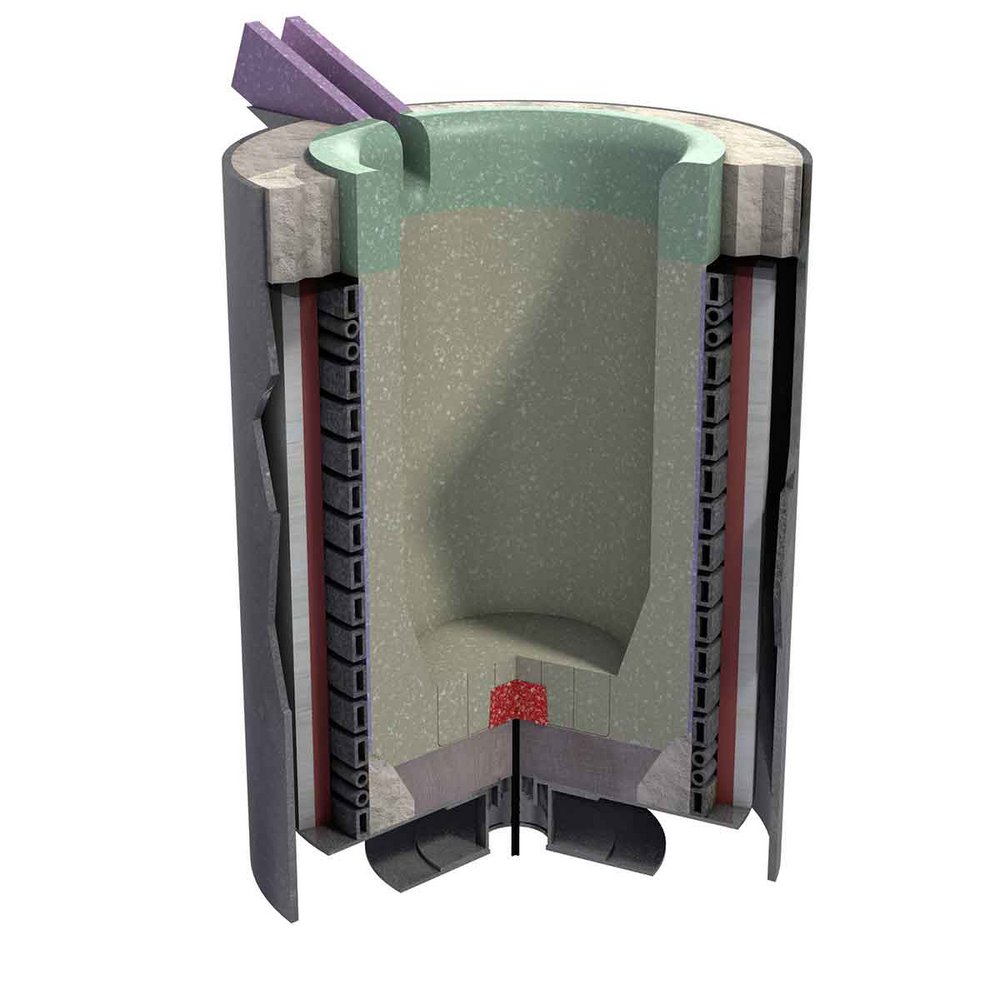
How to prevent casting defects: furnace refractory linings
Coreless induction furnaces (CIF) comprise the vast majority of furnaces used in the steel foundry sector. While a range of factors play into the optimal running of these furnaces, the refractory lining system is the basis for success.
Refractory linings have two main jobs: firstly to protect furnace parts from the extreme heat and aggressive chemistry of the steel melt; and secondly, to keep as much of that heat within the process as possible, and so help maximise the thermal efficiency of the casting process. These roles expose refractory linings to significant thermal and chemical stresses. They are also vulnerable to mechanical abrasion during furnace charging.
These extreme conditions can cause the refractory lining to wear into and contaminate the melt, which may cause casting defects known as inclusions. From a clean casting perspective, the refractory lining needs to offer high levels of resistance to thermal, chemical and mechanical attack. This is particularly relevant for the working lining: the part that is exposed to direct contact with the melt.
How to prevent casting defects: purge plugs
Porous purge plugs (or gas diffusers) are optional lining components that allow the injection of an inert gas, such as argon, into the melt – with two major benefits.
Purging helps to degas the melt, which helps limit the formation of oxides, which are principally responsible for slag-line erosion of the refractory lining. This reduces the risk of chemical wear and refractory inclusions contaminating the melt, not only in the furnace but also in downstream processes where refractory linings are present (e.g., ladles, stopper rods, and nozzles).
Degassing also helps to reduce the occurrence of gas porosity defects. These are caused by the release of gas during solidification of the molten metal in the mould (solids being unable to hold as much gas as liquids). The lower the gas content of the melt, therefore, the less risk of gas porosity defects.
Secondly, purging improves mixing of the melt, creating a more thermally and chemically homogenous melt. This enables a more even distribution of alloying components and deoxidisers.
Refractory lining systems from Foseco
Foseco offers a complete range of refractory lining materials for induction furnaces. For example, KELLUNDITE spinel-forming, high alumina dry-vibratable working linings are specifically designed to achieve high resistance to slag and thermal wear. Or TRIAD Z 230 a new no cement castable based on ultra-high alumina (94%) aggregate with superior slag and abrasion resistance.
We also offer porous purge plug systems for all furnace sizes and capacities and for use with our full range of linings, including KELLUNDITE.
Foseco refractory linings can make a significant difference when it comes to casting clean. Ultimately, however, selection of the appropriate solutions will depend on your specific foundry conditions and casting application. Expert advice will assist in formulating process-specific strategies for optimal results.
Discover more about common steel casting defects and the solutions available to prevent them in our white paper: Casting clean: today’s solutions and opportunities.