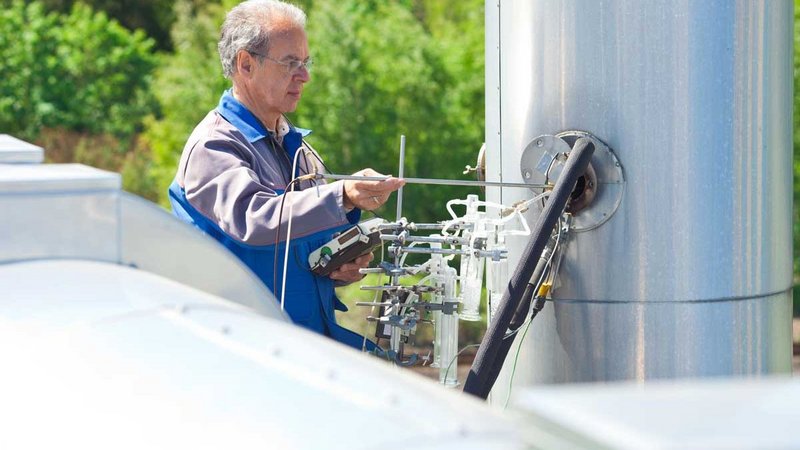
Steel castings
-
Steel castings range in size from a few grams to hundreds of tonnes. Steel castings are often used in critical situations where optimum mechanical properties are essential so that freedom from casting defects is particularly important. The advantages of cast steel over other cast metals, such as ductile iron, are:
- High modulus – minimizing deflection under heavy static loading
- Shock and impact resistance – to cope with severe dynamic loading
- Heat-treatable – to give the required toughness, hardness, and strength
- Weldable – so that castings can be joined to wrought steel products
- High temperature strength – special alloys are available
Steel castings compete in many areas with steel weldments. In welding, it is difficult to avoid stress concentrations at junctions while castings have well-radiused joints so that fatigue resistance of cast steel junctions is superior to that of welded junctions. Also welds, especially in large structures, are not always amenable to stress-relieving after welding so that internal stresses are likely to be greater in weldments than in steel castings. This may lead to distortion of weldments or even failure in highly stressed components.
Castings allow freedom of design which is not possible with weldments.
The main applications of steel castings are:
- Valves, pumps, and compressors
- Construction and earth moving equipment
- Crushing, grinding, quarrying, and dredging
- Oil and gas rigs
- Mining equipment
- Motor vehicles
- Defence equipment
- Railways